THE ANONYMOUS
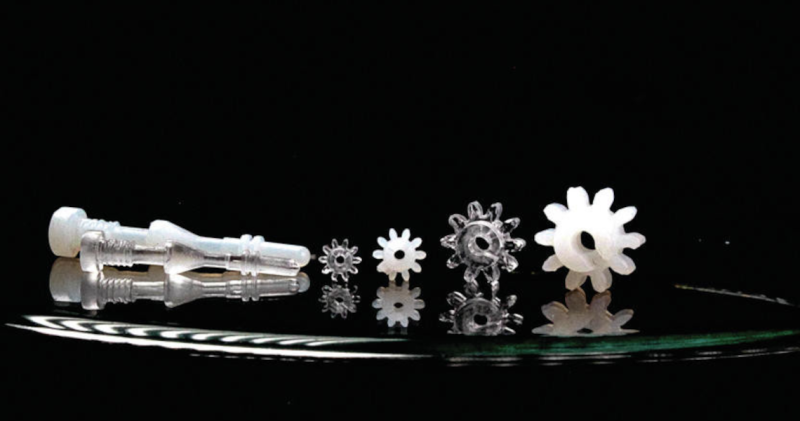
Glass is one of humanity’s oldest materials, and it is still used widely for everything from drinking vessels and packaging to optics and communications. Unfortunately, the methods for working with glass are stuck in the past. Most methods require a lot of high heat in the range of 1500 °C to 2000 °C, and they’re all limited in the complexity of shapes that can be made.
As far as making shapes goes, glass can be blown and molten glass pressed into molds. Glass can also be ground, etched, or cast in a kiln. Glass would be fantastic for many applications if it weren’t for the whole limited geometry thing. Because of the limitations of forming glass, some optic lenses are made with polymers, even though glass has better optical characteristics.
Ideally, glass could be injection molded like plastic. The benefits of this would be twofold: more intricate shapes would be possible, and they would have a much faster manufacturing time. Well, the wait is over. Researchers at Germany’s University of Freiburg have figured out a way to apply injection molding to glass. And it’s not just any glass — they’ve made highly-quality, transparent fused quartz glass, and they did it at lower temperatures than traditional methods. The team used x-ray diffraction to verify that the glass is amorphous and free of crystals, and were able to confirm its optical transparency three ways — light microscopy, UV-visible, and infrared measurements. All it revealed was a tiny bit of dust, which is to be expected outside of a clean room.
Polymers Make it Possible
This is exciting news for two big reasons: injection molding opens the door to complex shapes, and it’s also less energy-intensive than traditional glass forming methods. The team began this journey in 2017 by hacking a 3D printer to squirt glass paste instead of plastic. To do this, they made a printable powder from silica nanoparticles and a UV-curable polymer. While it certainly worked for making complex shapes, printing and curing was a slow, one-at-a-time process.
But now they have upgraded the process to work with injection molding. So what’s the secret? More space-age polymers. They started again with silica nanoparticles and added polyethylene glycol (PEG) and polyvinyl butryal (PVG). This produced a paste which they fed into an extruder, and the extruder squirted the plasticized glass into small intricate molds shaped like tiny gears, discs, and rooks.
Once they come out of the mold, the pieces hold themselves together thanks to the van der Waals interactions that occur between silica particles. These are weak electrostatic forces that bind molecules to one another. For a more permanent bond, the researchers first soak the pieces in water for several hours to wash away the PEG. Then they fire the pieces in two stages — once at 600° C to burn away the PVB, and a second time at 1300° C to fuse the silica particles together. At this point, the plastic is gone, and all that remains is glass.
Dr. Frederik Kotz, one of the researchers and group leader at materials startup Glassomer had this to say about their discovery:
We see great potential, especially for small high-tech glass components with complicated geometries. In addition to transparency, the very low coefficient of expansion of the glass also makes the technology interesting. Sensors and optics work reliably at any temperature if the key components are made of glass.
A New Class of Fast Glass
Although injection molding is faster than the team’s printing-and-curing process from a few years ago, there’s one catch: washing away the PEG has to be done over a number of days to keep the glass from cracking. Surely someone will come up with a way to do it faster. Maybe even before the next time the world needs glass vials for billions of doses of a new vaccine.
Images via Glassomer
from Hackaday https://ift.tt/3pHhoed
No comments: